COB Lighting Heat Dissipation: A Comparative Analysis of Silicone Thermal Pads and Thermal Grease
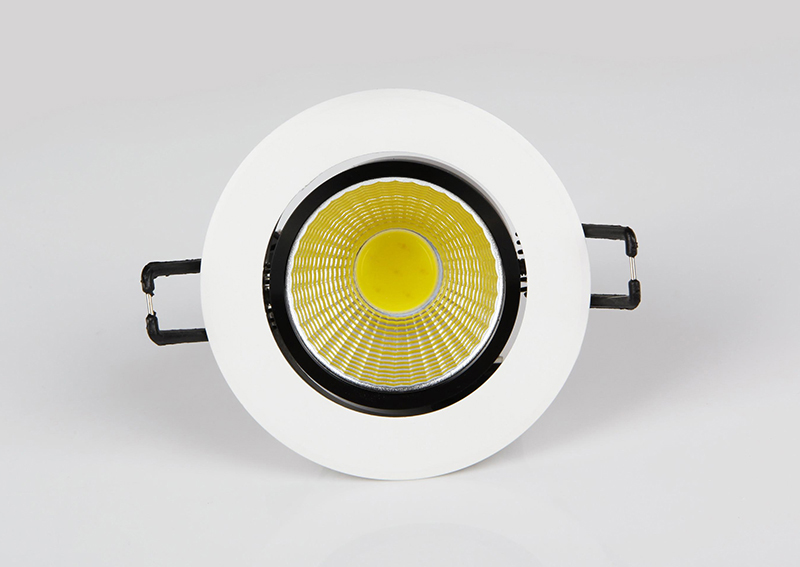
Before discussing the choice between silicone thermal pads and thermal grease, it’s essential to understand what COB (Chip On Board) technology is and the heat dissipation challenges it faces.
What is COB?
COB (Chip On Board) is an advanced packaging technology that directly mounts multiple bare chips (dies) onto a circuit board and then electrically connects them to the substrate through conductive connections. This reduces the length of interconnects between chips, improves signal transmission efficiency, and significantly reduces the overall size of the device.
COB technology is widely used in high-density integrated circuits, LED lighting, camera modules, and more. Its main advantages include:
● High-density packaging: Multiple chips are integrated into one substrate, enabling higher functionality in limited space.
● Simplified design: Multiple chips are mounted directly on the PCB, reducing complex packaging steps and costs.
● Lower inductance and capacitance: The shorter connection distance between the chips and the substrate reduces unnecessary inductance and capacitance, enhancing performance.
However, while COB technology has significant advantages in performance and packaging, it also brings new challenges in heat dissipation.
Heat Dissipation Challenges of COB
1. High Power Density Leading to Heat Dissipation Issues
COB technology integrates multiple chips within one package, making the space between the chips compact and leading to heat concentration. The high power density means a large amount of heat is generated per unit area, and if not dissipated efficiently, the chip temperature can rise rapidly, affecting performance stability or even causing thermal failure.
2. Complex Thermal Conduction Path
In COB packaging, multiple chips need to dissipate heat simultaneously. The surface shape and height of each chip may not be identical, adding complexity to the heat conduction path. Traditional thermal design may not effectively handle such irregular environments, requiring efficient thermal materials to fill these gaps.
3. High Temperature Requirements for Material Stability
The chips in COB technology operate at high temperatures for extended periods, necessitating that thermal materials not only provide high thermal conductivity but also maintain long-term stability without degrading performance in high-temperature environments. Therefore, the thermal material's heat resistance and aging performance must be considered.
4. Size and Structural Limitations
Due to the compact design of COB packaging, the space for heat sinks is often limited. Lightweight and efficient thermal materials are necessary to optimize heat dissipation. Additionally, the material’s electrical insulation and mechanical strength are equally important to avoid interference with circuits or damage due to pressure.
Faced with these heat dissipation challenges, choosing the right thermal material is critical. Silicone thermal pads and thermal grease, as two commonly used thermal interface materials, can help address some of these issues. Next, we’ll compare these two materials in detail, analyzing their advantages and disadvantages in COB heat dissipation.
Overview of Silicone Thermal Pads and Thermal Grease
1. Silicone Thermal Pads
Silicone thermal pads are sheet-like materials composed of silicone and thermal fillers, offering excellent thermal conductivity and electrical insulation. Their advantages include:
● Strong stability: Silicone thermal pads maintain structural integrity and do not deform due to temperature fluctuations.
● Even thickness: The thickness of silicone pads can be precisely controlled, which is essential for ensuring consistent thermal paths.
● Easy installation and maintenance: Their solid form makes installation more convenient, and they are easy to replace and maintain.
● Durability and aging resistance: Silicone thermal pads are resistant to aging and do not dry out or fail, making them suitable for devices requiring long-term stable heat dissipation.
2. Thermal Grease
Thermal grease is a paste-like thermal interface material composed of silicone oil and thermal fillers, mainly used to fill small gaps between heat sources and heat sinks. Its characteristics include:
● High thermal conductivity: Thermal grease offers high thermal conductivity, effectively reducing thermal resistance and improving heat dissipation.
● Adapts to complex surfaces: Due to its paste form, thermal grease fills irregular surfaces and gaps, ensuring full contact between interfaces.
● Relatively low cost: Compared to silicone thermal pads, thermal grease is generally more affordable, making it cost-effective for mass production.
Key Considerations for COB Lighting Heat Dissipation
The high power density of COB lighting makes effective thermal design crucial for ensuring performance and longevity. When selecting thermal materials, several factors should be considered:
● Thermal efficiency: The primary task of thermal materials is to quickly transfer the heat generated by LED chips to the heat sink or outer casing to prevent heat buildup.
● Long-term stability: COB lighting requires continuous operation for extended periods, so the long-term stability and anti-aging properties of the thermal material are critical.
● Ease of installation: The compact structure of COB chips requires the installation of thermal materials to be as simple as possible, ensuring that they do not affect the design and assembly efficiency of the lighting system.
● Cost control: For mass-produced LED lighting, the cost-effectiveness of thermal materials must be considered, especially in large-scale manufacturing.
Comparison of Silicone Thermal Pads and Thermal Grease in COB Lighting
1. Thermal Performance
Thermal grease typically offers higher instantaneous thermal conductivity, making it suitable for high-power devices requiring rapid heat dissipation. Its flowability allows it to fill irregular interfaces better, reducing thermal resistance and maximizing heat transfer. However, silicone thermal pads also provide solid thermal performance, especially in scenarios requiring long-term stable heat dissipation, where the thermal conductivity remains consistent.
2. Service Life
Over time, thermal grease may dry out or overflow, especially in high-temperature environments, which can reduce its effectiveness. In contrast, silicone thermal pads have better heat and aging resistance, maintaining stability without material degradation or performance loss. For long-term applications in COB lighting, silicone thermal pads offer a more reliable solution.
3. Ease of Installation
Due to its solid sheet structure, silicone thermal pads are easier to cut and install, adapting well to the shape and size of COB lighting. Thermal grease, on the other hand, requires precise application during installation to avoid overuse or underuse, complicating the process. Additionally, the stickiness of thermal grease can cause contamination or make cleaning difficult, which is inconvenient during maintenance.
4. Cost Comparison
Generally, thermal grease is more affordable than silicone thermal pads, particularly in mass production, where its cost advantages become apparent. However, considering the maintenance and replacement costs in long-term use, silicone thermal pads may offer greater economic efficiency throughout the product lifecycle.
Recommendations for Choosing Thermal Materials for COB Lighting
In the heat dissipation design of COB lighting, silicone thermal pads and thermal grease each have their advantages and applicable scenarios. If the lighting requires high power and rapid heat dissipation, and cost is a major concern, thermal grease may be the better option. However, for high-end COB lighting systems that require long-term stable operation with minimal maintenance, silicone thermal pads provide a more reliable heat dissipation solution.
Conclusion
In conclusion, the choice of thermal materials for COB lighting should be based on the actual application requirements. Silicone thermal pads, with their stability, long lifespan, and ease of installation, are ideal for high-end lighting systems requiring continuous stable heat dissipation. On the other hand, thermal grease, with its high thermal conductivity and cost advantages, is more suitable for short-term, cost-sensitive applications. Designers should consider factors such as power, operating environment, production cost, and maintenance needs to make the best choice for optimizing the performance and lifespan of COB lighting systems.