BMS (Battery Management System) indeed employs certain silicone thermal interface materials in its design and manufacturing process to optimize its thermal management performance. These choices of thermal materials aim at enhancing the heat dissipation efficiency of the battery system, ensuring that the battery operates within an appropriate temperature range during its service life, thus extending the battery's lifespan and improving overall performance.
It is well-known that BMS is crucial for modern electronic devices, functioning as a smart brain that precisely regulates the flow of energy in batteries. However, what specific silicone thermal interface materials does BMS rely on to ensure battery safety and performance stability? This is an intriguing question because different manufacturers, product models, and application scenarios may opt for different materials.
Today, Nfion, a manufacturer of thermal interface materials, will lift the veil on this mystery by introducing the top 7 silicone thermal interface materials commonly used in BMS systems. These materials serve as guardians for the BMS, silently protecting battery safety and efficiency, making our lives more convenient and efficient.
Let us look forward to exploring these miraculous silicone thermal interface materials together and appreciating the infinite possibilities they bring to modern technology.
A soft and elastic thermal management material, the thermal conductive silicone pad fills gaps between battery cells or between the battery and cooling components, effectively conducting heat while also providing insulation and shock absorption.
Thermal grease can be applied between BMS components and cooling elements to reduce contact thermal resistance, enhance heat transfer efficiency, and maintain excellent electrical insulation properties.
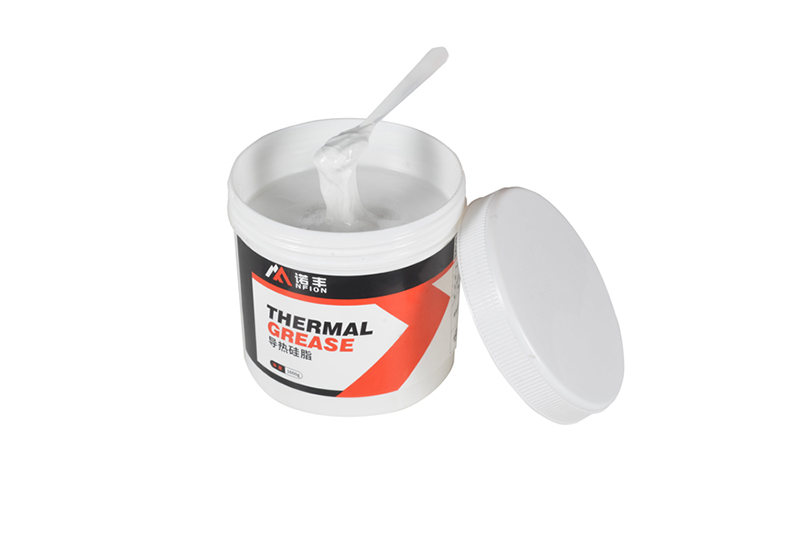
3.Thermal Conductive Silicone Gel:
A single-component thermal compound, thermal conductive silicone gel boasts high thermal conductivity, low thermal resistance, and good electrical insulation, evenly distributing internal battery heat throughout the entire battery pack, preventing localized overheating that could lead to decreased battery performance.
This material possesses exceptional thermal conductivity, insulation, damping, and flame retardant properties, suitable for irregular gaps between battery modules, facilitating heat transfer between the battery pack and the cooler while forming an electrical insulation layer and cushioning layer, thereby protecting the battery pack and prolonging its lifespan.
5. Thermal Insulation Sheet:
Thermal insulation sheets effectively dissipate heat from the BMS, lowering the operating temperature of battery components, which in turn enhances battery stability and extends its life. During the BMS operation, battery modules generate heat; if not dissipated promptly, it might cause a decline in battery performance or pose safety hazards. The thermal conductivity of the insulation sheet helps address this issue, keeping the battery within an optimal working temperature range.
These thermal insulation sheets not only provide thermal conductivity but also exhibit outstanding electrical insulation properties. In the BMS, there's a need for good insulation between components to prevent issues such as current leakage or short circuits. Thermal insulation sheets offer an effective insulating barrier, ensuring electrical safety within the BMS.
6.Thermal Adhesive:
With excellent thermal conductivity, thermal adhesive efficiently transfers heat generated by battery modules during the BMS operation, maintaining battery stability and extending its life. Moreover, it has strong adhesive capabilities, bonding various materials within the BMS (such as metals, ceramics, plastics, etc.) securely, ensuring solid connections between components. This adhesive property not only strengthens the overall structural integrity of the BMS but also prevents component loosening or damage due to vibration or impact.
Furthermore, thermal adhesive features flame retardancy, moisture resistance, shock resistance, and insulation, which further enhance the safety and reliability of the BMS. Its flame retardancy can mitigate fire risks, while its moisture and shock resistance properties help protect the BMS from harsh environmental conditions.
7.Thermal Potting Compound:
Organic silicone thermal potting compounds form a soft, elastic, and adhesive surface upon curing at room temperature, offering excellent electrical insulation properties. For BMS electronic modules requiring dust-proofing, water resistance, shock resistance, and superior heat dissipation, thermal potting with silicone can encapsulate the entire module, safeguarding internal components while effectively conducting heat.
In BMS, the primary role of these silicone thermal materials is to improve the battery's heat dissipation efficiency, ensuring safe operating temperatures and thereby extending battery life and enhancing overall electric vehicle performance. Notably, Nfion's NF150 series thermal materials, with their exceptional thermal conductivity and diverse physical characteristics, have been widely adopted in BMS, effectively transferring heat generated by both the battery and BMS, ensuring stable battery performance.
These silicone thermal materials can be customized according to practical application needs, with varying hardness, thickness, thermal conductivity, pressure resistance levels, flame retardancy ratings, and temperature ranges to meet the thermal management requirements of different BMS systems.
It's important to note that designing and manufacturing a BMS is a complex process, where besides selecting thermal materials, factors such as battery type, capacity, operating voltage, and working environment must also be considered. Therefore, the specific selection and usage plan for thermal materials should be designed and optimized by professional engineers based on actual needs.
Moreover, with the continuous advancement of technology, new thermal materials and techniques are constantly emerging. Hence, for BMS manufacturers, staying up-to-date with the latest technologies and materials in the thermal management field, continuously optimizing product thermal performance, is a critical means to enhance product competitiveness and market share.