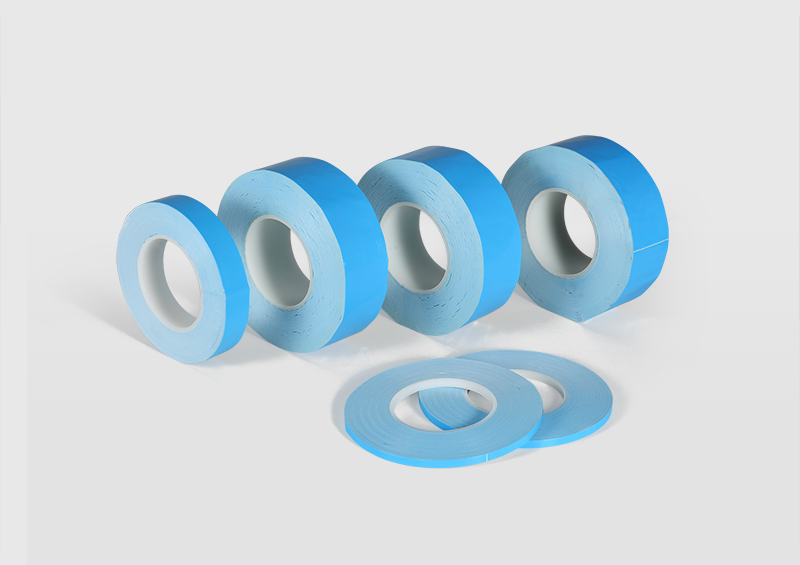
Definition:
Thermal conductive double sided tape is a specialized adhesive tape specifically designed for transferring heat within electronic devices and other systems requiring thermal management. Its primary characteristic is its dual-sided adhesiveness, enabling the formation of a secure bond between two contacting surfaces while also exhibiting excellent thermal conductivity.
Structure & Composition:
Typically, thermal conductive double sided tape consists of a three-layer structure: a central thermally conductive adhesive layer sandwiched between two pressure-sensitive adhesive layers. The conductive adhesive layer contains high-performance fillers (such as ceramic powders, graphite, or metal oxides) dispersed in an organic polymer matrix (e.g., silicone rubber, acrylates), which imbue the tape with exceptional thermal conductivity. The pressure-sensitive adhesive layers provide bonding properties, allowing the tape to adhere firmly to both the heat source (e.g., integrated circuits, LED packages, power devices) and the heat dissipation device (e.g., heat sinks, radiators, metal enclosures).
Thermal Conduction Principles:
1. Thermal conduction: The core constituents of thermal conductive double sided tape include high-conductivity fillers (such as ceramic powder, graphite, or metal oxides), which possess high thermal conductivity and efficiently transfer heat. When a heat source (like an LED chip or CPU) generates heat, it is first transferred through direct contact to the thermal conductive double sided tape. The close contact between filler particles and their integration with the substrate (e.g., glass fiber cloth) create a continuous thermal conduction path, enabling heat to travel along the tape from the heat source side to the heat dissipation device (e.g., a heatsink).
2. Interface filling: Thermal conductive double sided tape possesses a certain degree of softness and compressibility, allowing it to fill microscopic gaps and irregularities present between the heat source and the heat dissipation device. This attribute helps eliminate air gaps at the interface, as air is a poor thermal conductor that hinders efficient heat transfer. By filling these gaps, the tape establishes a low thermal resistance contact interface, enabling heat to directly pass from the heat source to the heatsink without being impeded by an air layer, significantly enhancing thermal conduction efficiency.
3. Thermal radiation & convection assistance: Although not the primary mode of heat transfer, in some cases, thermal conductive double sided tape can also aid cooling through its own weak thermal radiation effect and by assisting in enhancing heat convection. When the tape itself or the surfaces in contact with it become warmer, they emit some heat in the form of infrared radiation. Moreover, if the heat dissipation device features ventilation channels or is subject to external convection conditions, the tape helps maintain good contact between the heat source and the heatsink, facilitating more effective removal of heat by air or coolant.
4. Structural stability & long-term reliability: The strong adhesion of thermal conductive double sided tape ensures a long-lasting, secure connection between the heat source and the heat dissipation device, preventing interface separation due to mechanical vibration, temperature cycling, and maintaining a stable thermal contact area. This stable thermal contact is crucial for sustained, efficient heat conduction, helping to prevent increased thermal resistance and reduced cooling efficiency caused by poor contact.
In summary, thermal conductive double sided tape utilizes its internal high-conductivity fillers for heat conduction, employs its softness and compressibility to eliminate air gaps between the heat source and the heat dissipation device to boost heat transfer efficiency, and maintains a stable thermal contact interface to ensure long-term, reliable thermal management performance. These principles collectively enable the tape to effectively transfer heat from the heat source to the heat dissipation device in various electronic devices and LED lighting applications, ensuring the operating temperature remains within safe limits, extending equipment lifespan, and enhancing performance stability.
Key Characteristics of Thermal Conductive double sided Tape:
1. Dual-sided adhesion: This type of tape has adhesive properties on both sides, enabling it to securely bond two different components simultaneously.
2. Efficient thermal conductivity: Thermal conductive double sided tape contains high-conductivity fillers, such as thermally conductive ceramic powders or high-conductivity material coatings, which endow the tape with superior thermal conductivity capabilities. It can effectively transfer heat generated by heat sources (e.g., microprocessors, LED chips, power modules) rapidly to heat dissipation devices (e.g., heatsinks, radiators, metal enclosures), thereby helping to maintain the normal operating temperature of electronic devices and preventing overheating-induced performance degradation or failure.
3. Flexibility & adaptability: Thermal conductive double sided tape usually exhibits a certain degree of softness and elasticity, allowing it to accommodate components with various shapes and surface roughnesses, filling gaps between them and providing good contact areas to ensure unimpeded heat transfer paths. This makes it easy to apply in irregular surfaces, confined spaces, or complex structures.
4. Bonding strength: In addition to its thermal conductivity function, thermal conductive double sided tape possesses high bonding strength, ensuring that bonded components remain stably connected under various working conditions (e.g., vibration, impact, temperature changes), while also preventing interface separation due to mechanical stress, which could affect cooling performance.
5.Process convenience: As a pressure-sensitive tape, thermal conductive double sided tape requires no curing or heating for immediate adhesion, simplifying assembly processes, reducing production costs, and making it easily removable or replaceable, particularly suitable for equipment that requires regular maintenance or upgrades.
Classification of Thermal Conductive double sided Tapes:
Thermal conductive double sided tapes come in a wide variety, which can be classified based on their constituent materials, structural characteristics, and application requirements.
1. By Substrate Type:
No Substrate: Comprised solely of the thermal adhesive layer, with no additional supporting substrate, offering exceptional thermal conductivity and low thermal resistance, ideal for lightweight and ultra-thin devices, as well as applications demanding utmost thermal efficiency.
Glass Fiber Cloth Substrate: The adhesive layer is coated onto a glass fiber cloth, providing good mechanical strength and heat resistance, while maintaining satisfactory thermal conductivity. Suitable for applications requiring moderate strength support and high-temperature resistance.
Aluminum Foil Substrate: The adhesive layer is attached to aluminum foil, enhancing the ability to reflect thermal radiation, contributing to further improved heat dissipation. Commonly used in applications necessitating efficient cooling and electromagnetic shielding.
2. By Filler Type:
Ceramic Powder-filled: Filled with high thermal conductivity ceramic powders such as alumina, boron nitride, or zirconia, offering outstanding thermal conduction properties.
Graphite-filled: Utilizing the layered structure and high thermal conductivity of graphite, resulting in ultra-low thermal resistance thermal conductive tapes.
Metal Oxide-filled: Containing metal oxides like alumina or zinc oxide, providing good thermal conductivity and a certain level of electrical insulation.
3. By Thickness and Hardness:
Various Thicknesses: Thermal conductive double sided tapes are available in multiple thickness specifications, e.g., 0.1mm, 0.15mm, 0.25mm, to cater to diverse cooling demands and gap-filling requirements.
Soft vs. Hard: Depending on the hardness requirement of the application, there are soft thermal conductive double sided tapes (easily conforming to uneven surfaces) and hard ones (providing stronger mechanical support).
4. By Special Properties:
Non-silicone: Free of silicone content, suitable for applications sensitive to silicone or requiring no silicone oil evaporation, such as semiconductor manufacturing, optical equipment, etc.
UV-resistant: Possessing UV-resistant properties, applicable for outdoor or prolonged exposure to UV light in LED lighting, photovoltaic applications, etc.
Electrically Insulating: In addition to thermal conductivity, these tapes offer high electrical insulation, suitable for applications requiring isolation from high-voltage fields or prevention of short-circuits.
High-Temperature Resistant: Designed specifically for electronic devices operating in high-temperature environments, these tapes maintain stable thermal conductivity and bonding strength at elevated temperatures.
Application fields of heat-conducting double sided tape
Thermal conductive double sided tapes, with their exceptional thermal conductivity, excellent adhesion, and ease of use, find widespread applications across numerous domains.
1. Electronics & Information Technology Industry:
Computer Hardware: Used for bonding CPUs, GPUs, memory modules, northbridge/southbridge chips, etc., to heat sinks, ensuring efficient cooling and preventing overheating-induced system instability or damage.
Consumer Electronics: Within smartphones, tablets, game consoles, etc., employed for adhering batteries, power management modules, display driver boards, etc., to heat sinks or heat frames.
Telecommunication Equipment: In switches, routers, base stations, etc., utilized for thermal management of power amplifiers, power modules, etc.
Industrial Control & Automation Equipment: In PLCs, servo drives, inverters, etc., used for bonding heat-generating components to cooling devices, ensuring long-term stable operation.
2. LED Lighting Industry:
LED Lamps: Employed for fixing and conducting heat from LED chips to aluminum substrates or heat sinks, particularly suitable for high-power LED lighting products such as streetlights, stage lights, spotlights, etc.
LED Displays: In indoor/outdoor display modules, used for bonding LED packaging units to heat sink backplates, ensuring effective cooling during high-brightness operation.
3. Automotive Electronics:
Powertrain Systems: Used in EVs and HEVs for thermal management of critical components like PCUs, inverters, BMS, etc.
In-Vehicle Entertainment & Information Systems: In car navigation, audio systems, displays, etc., employed for thermal management, ensuring stable operation of in-car electronic devices.
4. New Energy Fields:
Photovoltaics: In solar cell modules, used for bonding solar cells to heat sink backplates, improving thermal management, enhancing power generation efficiency, and prolonging component life.
Energy Storage Systems: Serving as thermal interface materials between battery cells or connecting battery cells to heat sinks, effectively managing heat generated during charging and discharging.
5. Home Appliances:
Televisions & Monitors: Used for cooling backlight modules, power modules, etc., in LCD or OLED panels.
Air Conditioners & Refrigerators: Employed for bonding heat-generating parts like variable frequency drive circuits, power modules, etc., to heat sinks.
6. Medical Devices:
In portable medical devices, imaging diagnostic equipment, etc., used for cooling electronic components, ensuring reliability and safety under high-intensity operation.
7. Aerospace & Defense:
In satellites, radar, avionics equipment, etc., in high-reliability environments, used for thermal management of precision electronics.
In summary, thermal conductive double sided tapes are widely used in any scenario involving thermal management of electronic devices, especially in compact designs, high-power density systems, and those requiring rapid response and good thermal stability. With the continuous development of electronic technology and increasing demands for device miniaturization and efficiency, the application scope of thermal conductive double sided tapes will continue to expand and deepen.
Selection of Thermal Conductive double sided Tapes:
When selecting thermal conductive double sided tapes, several factors must be considered holistically to ensure they meet specific application requirements.
1. Thermal Management Needs:
Heat Source Power: Understand the amount of heat generated by the heat source, and accordingly choose a tape with a high enough thermal conductivity (W/m.K) to ensure rapid and effective heat transfer.
Operating Temperature Range: Confirm the operating temperature range of the device, and select a tape that maintains stable performance within this range and has the required temperature rating.
Thermal Resistance Requirements: Calculate the required thermal resistance value and opt for a tape with low thermal resistance to minimize heat loss during transfer.
2. Physical Properties & Compatibility:
Thickness & Size: Based on the gap size and device structure in the application, choose a tape of appropriate thickness to ensure good contact and thorough heat transfer. Also, ensure the tape width and length meet assembly requirements.
Adhesion Strength: Evaluate the tape's adhesion performance to the heat source and heat sink surfaces, ensuring stable bonding under operating temperatures and environmental conditions, preventing thermal contact degradation due to adhesive failure.
Flexibility & Shear Strength: For applications involving curved, uneven surfaces, or dynamic loads, choose a tape with good flexibility and appropriate shear strength to accommodate complex shapes and withstand mechanical stresses.
Compatibility: Consider whether the tape is compatible with the contact surface materials (e.g., metals, plastics, ceramics), avoiding chemical reactions or corrosion issues.
3. Electrical Properties:
Electrical Insulation: If electrical insulation is required between the heat source and heat sink, ensure the selection of a tape with high insulation resistance and suitable dielectric strength to prevent short-circuit risks.
EMI Protection: For applications with EMI shielding needs, choose tapes featuring metal substrates (e.g., aluminum foil) or possessing electromagnetic shielding capabilities.
4. Environmental Adaptability:
Weather Resistance: If the product is to be used outdoors, in high temperatures, humidity, low temperatures, or other special environments, select tapes with corresponding weather resistance (e.g., UV resistance, moisture resistance, high/low-temperature resistance).
Environmental Compliance: Consider whether the tape complies with environmental regulations such as RoHS, REACH, especially for export or specific industry applications.
5. Cost & Supply:
Cost-effectiveness: While meeting performance requirements, compare prices of different brand and model tapes, considering overall cost-effectiveness, including material costs, processing costs, and potential long-term maintenance costs.
Supplier Reliability: Choose a supplier with a good reputation, consistent product quality, and robust technical support, ensuring supply chain stability and after-sales service.
6. Testing & Certification:
Sample Testing: Before large-scale application, conduct necessary sample tests to verify the tape's thermal performance, adhesion durability, and longevity under actual application conditions.
Industry Standards & Certifications: Check whether the tape complies with relevant industry standards (e.g., UL, IPC) or obtains certifications for specific application fields (e.g., AEC-Q200 in the automotive industry), ensuring compliance with application specifications.
The selection of thermal conductive double sided tapes is a systematic process that involves comprehensive consideration of thermal management performance, physical properties, electrical properties, environmental adaptability, cost & supply, and testing & certification. In practice, detailed technical exchanges with suppliers should also be conducted to obtain professional selection advice and support. If you're seeking an exceptional choice in thermal conductive double sided tapes, Nfion Thermal is your trusted partner. At your command, we will respond swiftly like a gust of wind, presenting you with meticulously crafted thermal conductive double sided tape solutions.