In the rapid development of modern industrial automation and power electronics technology, inverters play a crucial role as the key devices controlling the speed and torque of motors. The stability and operational efficiency of inverters directly impact the reliability and efficiency of the entire system. However, as the power density of inverters continues to increase, thermal management issues have become increasingly prominent, emerging as a critical factor limiting their performance and the expansion of their application range. Thermal grease, as an efficient thermal interface material, plays an indispensable role in addressing the cooling challenges of inverters.
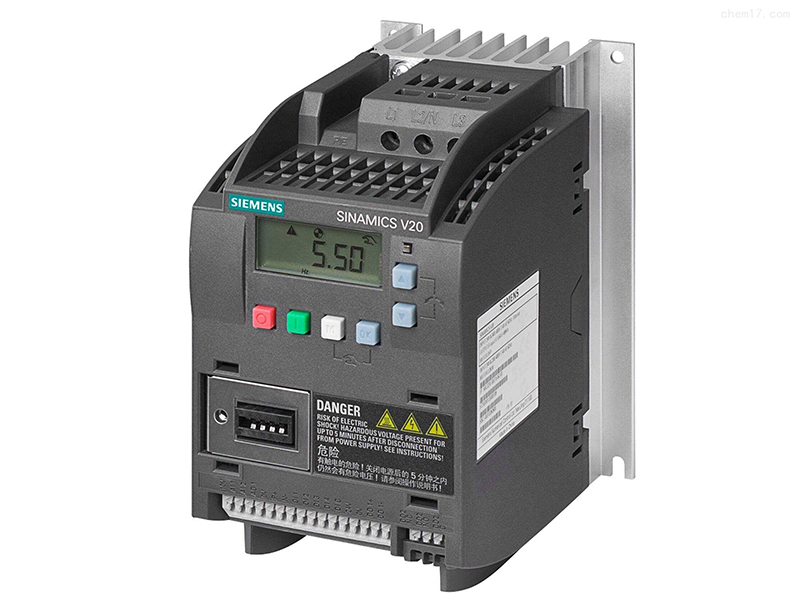
What is an Inverter?
An inverter, also known as a Variable Frequency Drive (VFD), is a device used to control the speed and torque of an AC motor. By adjusting the frequency and voltage of the power supplied to the motor, it can control the motor’s speed, achieve energy savings, precise control, and extend the lifespan of the equipment.
Working Principle of an Inverter
The basic working principle of an inverter involves converting AC power with fixed frequency and voltage into AC power with adjustable frequency and voltage. The core steps include:
1. Rectification: The input AC power is converted into DC power, usually accomplished through diodes or a rectifier bridge.
2. Filtering: The rectified DC power is typically not smooth and needs to be filtered to achieve a more stable current.
3. Inversion: The smooth DC power is then converted back to AC power, but this time with controllable frequency and voltage. The inverter achieves frequency and voltage regulation through a series of switches (such as IGBTs, Insulated Gate Bipolar Transistors) and Pulse Width Modulation (PWM) techniques.
4. Output: The converted AC power with adjustable frequency and voltage is supplied to the motor, controlling its speed and torque.
Main Functions of an Inverter
1. Speed Control: The inverter adjusts the motor’s speed by changing the output frequency, allowing precise control over various speeds. This is particularly important for industrial machinery requiring variable speed operations, such as conveyors, pumps, and fans.
2. Energy Saving: By regulating the motor speed, inverters can significantly reduce energy consumption, especially in applications requiring frequent starts or partial load operations.
3. Protection Functions: Inverters provide various protection functions, such as overcurrent, overvoltage, undervoltage, and overheating protection, ensuring the safety of both the motor and the system.
4. Soft Start and Stop: Inverters can achieve soft starting and stopping of the motor, preventing the current surges and mechanical stress associated with direct starting and stopping, thereby extending the equipment's lifespan.
Overview of Inverter Cooling Challenges
During operation, inverters generate significant heat due to the high-speed switching actions of internal power electronic components (such as IGBT modules). If this heat is not efficiently dissipated, it will lead to increased component temperatures, affecting their operational efficiency, reliability, and lifespan. Traditional air or liquid cooling methods can alleviate the thermal pressure to some extent, but their limitations are becoming more apparent in high power density, compact inverter designs. Therefore, finding more efficient heat transfer methods is crucial to resolving thermal management issues.
1. Enhancing Heat Transfer Efficiency
Inverter power components generate substantial heat during operation, which needs to be quickly conducted away by the heat sink to prevent excessive temperatures. Due to the inherent surface roughness of power components and heat sinks, tiny air gaps are often present. These air gaps have poor thermal conductivity, increasing thermal resistance and impeding heat transfer. Thermal grease effectively fills these gaps, significantly reducing interface thermal resistance, thus enhancing heat transfer efficiency and ensuring that power components operate within a safe temperature range.
2. Extending Equipment Lifespan
Excessive operating temperatures not only affect inverter efficiency but also accelerate the aging of internal components, shortening the equipment's lifespan. By effectively reducing the operating temperature of the inverter, thermal grease mitigates thermal stress on electronic components, thereby extending the equipment's lifespan. This is particularly important for industrial equipment that requires continuous operation, as it can significantly reduce failures and maintenance costs caused by overheating.
3. Improving Stability and Reliability
In industrial environments, inverters often need to operate under high load and high-temperature conditions, where changes in working conditions can exacerbate thermal issues. Thermal grease, with its excellent thermal stability and electrical insulation, maintains its thermal performance even in high-temperature environments, ensuring the stability and reliability of the equipment. The use of thermal grease can effectively prevent circuit failures and short-circuits caused by poor thermal management, enhancing the overall safety of the inverter system.
Selection and Application of Thermal Grease
1. Thermal Performance
The thermal conductivity coefficient is a crucial metric for evaluating thermal grease. Generally, the higher the thermal conductivity, the better the heat transfer performance of the material. When selecting thermal grease, it is essential to choose a product with an appropriate thermal conductivity coefficient based on the specific thermal management needs of the inverter to achieve optimal cooling performance.
2. Electrical Performance
Since inverters contain numerous circuits and electronic components, the electrical insulation performance of thermal grease is also a critical consideration. High-quality thermal grease should possess excellent electrical insulation properties to prevent short circuits or other electrical failures during application.
3. Durability and Environmental Adaptability
Inverters typically operate in complex industrial environments, making the durability and environmental adaptability of thermal grease extremely important. It is crucial to select thermal grease that can maintain stable performance in high-temperature, high-humidity, or highly corrosive environments to ensure its effectiveness throughout the equipment’s lifecycle.
In modern industry, as the application of inverters becomes increasingly widespread and their operating environments grow more complex, thermal management has emerged as a critical factor affecting equipment performance and lifespan. Thermal grease, with its excellent thermal conductivity, good electrical insulation, and strong environmental adaptability, has become the ideal material for addressing inverter cooling challenges. By selecting and applying thermal grease appropriately, companies can significantly improve the operational efficiency and stability of inverters, extend equipment lifespan, reduce maintenance costs, and ultimately achieve higher economic benefits. Therefore, paying close attention to the role of thermal grease in inverter design and maintenance is crucial for enhancing overall equipment performance.