Comparative Analysis of Thermal Conductivity between Alumina and Magnesia
In the realm of industrial materials and scientific research, alumina (Al₂O₃) and magnesia (MgO) are significant oxide materials widely used due to their exceptional physicochemical properties. This article will focus on comparing the thermal conductivity of these two materials, analyzing their advantages and disadvantages in different applications, and delving into their thermal conduction mechanisms.
Thermal Conductivity of Alumina
Basic Properties of Alumina
Alumina, with the chemical formula Al₂O₃, is a ceramic material known for its high hardness and melting point. It is commonly used in refractory materials, electronic components, and coatings. Its crystal structure is trigonal, providing excellent mechanical strength and corrosion resistance.
Thermal Conduction Mechanism of Alumina
The thermal conductivity of alumina primarily depends on its crystal structure and purity. In ideal conditions, alumina exhibits good thermal conductivity, mainly through lattice vibrations (phonon conduction). With high purity, alumina's thermal conductivity can reach up to 30 W/m.K. However, impurities and defects in practical applications can significantly reduce its thermal performance.
Influencing Factors
- Grain Size: Smaller grains increase grain boundary scattering, reducing thermal conductivity.
- Impurity Content: The presence of impurities introduces more phonon scattering centers, further lowering thermal conductivity.
- Temperature: As temperature rises, phonon-phonon scattering increases, leading to a decrease in thermal conductivity.
Thermal Conductivity of Magnesia
Basic Properties of Magnesia
Magnesia, with the chemical formula MgO, is a ceramic material characterized by a high melting point, high electrical resistivity, and good chemical stability. It is widely used in electrical insulators, refractory materials, and catalyst supports. Its crystal structure is cubic, with relatively low density.
Thermal Conduction Mechanism of Magnesia
Similar to alumina, the thermal conductivity of magnesia mainly relies on phonon conduction. In high purity and high crystallinity conditions, magnesia's thermal conductivity can reach up to 60 W/m.K, which is double that of alumina. The simplicity of its lattice structure and fewer defects help reduce phonon scattering, thus enhancing thermal conductivity.
Influencing Factors
- Crystal Purity: High purity magnesia has higher thermal conductivity; impurities significantly reduce its thermal performance.
- Temperature: As with alumina, increasing temperature boosts phonon-phonon scattering, decreasing thermal conductivity.
- Microstructure: The microstructural characteristics of magnesia (such as porosity and grain boundaries) significantly affect its thermal performance.
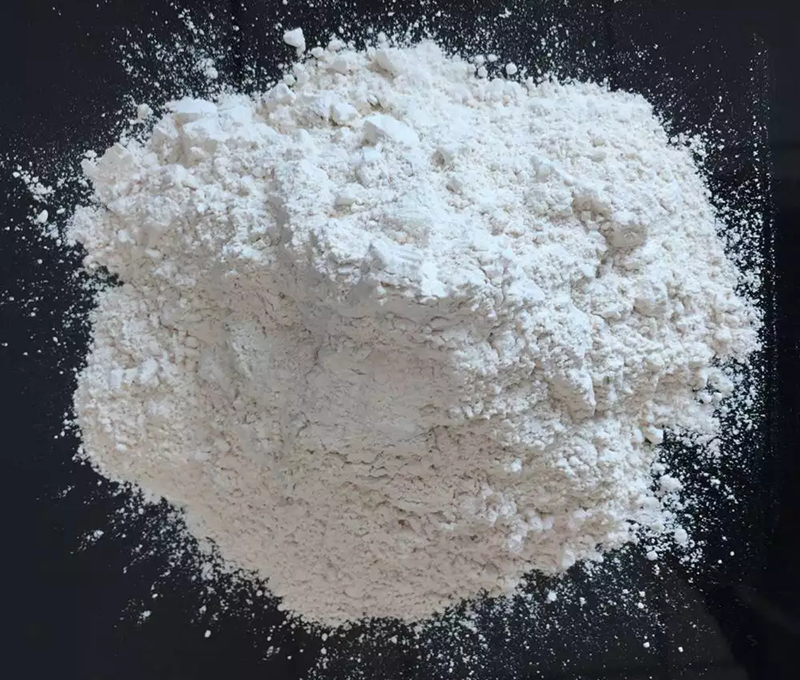
Comparison of Thermal Conductivity between Alumina and Magnesia
Thermal Conductivity Comparison
Under ideal purity and structural conditions, magnesia's thermal conductivity (about 60 W/m.K) is significantly higher than that of alumina (about 30 W/m.K). This difference is mainly due to their distinct crystal structures and impurity levels.
Application Scenarios Comparison
- High-Temperature Applications: In high-temperature conditions, magnesia often outperforms alumina due to its higher melting point (around 2800°C) and thermal conductivity, compared to alumina (melting point around 2050°C).
- Electronic Devices: Alumina is commonly used in electronic components and packaging materials due to its higher dielectric constant and mechanical strength, whereas magnesia is favored in applications requiring high thermal conductivity and insulation, such as high-power electrical appliances and heat sinks.
- Refractory Materials: Both materials are extensively used in refractory applications, but magnesia performs better in extremely high-temperature environments.
Cost and Processability
Alumina is generally more readily available and cost-effective than magnesia, and it is easier to process, making it advantageous for certain applications.
Conclusion
As crucial thermal materials, alumina and magnesia each have unique advantages and suitable application fields. Magnesia excels in high thermal conductivity and high-temperature applications, while alumina is widely used due to its good overall performance and cost-effectiveness. The choice between these materials should be based on specific application requirements, cost considerations, and performance needs.
By thoroughly understanding the thermal conduction mechanisms and influencing factors of these two materials, we can better utilize their properties to maximize their potential in industrial and research contexts.