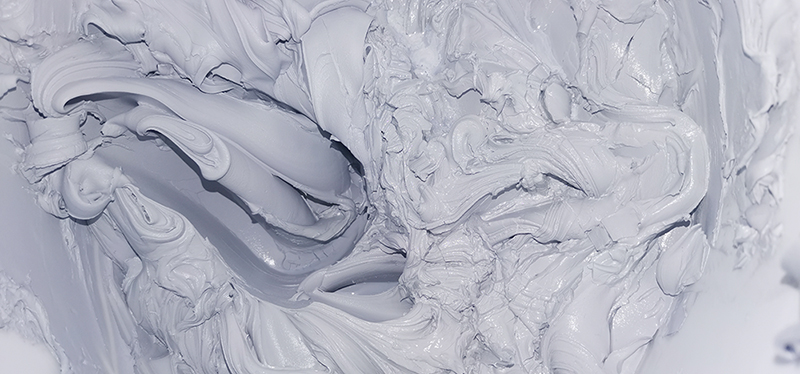
Thermal grease, also known as thermal paste or thermal compound, is a material used to enhance the thermal conductivity between electronic components and heat sinks. In modern electronic devices, where power density increases and sizes shrink, heat dissipation becomes increasingly critical. The performance of thermal grease directly influences cooling efficiency, thereby affecting the stability and lifespan of equipment. Specific gravity, a key physical characteristic of thermal grease that measures its density, is often discussed and analyzed. So, what exactly does the specific gravity of thermal grease mean, and how does it impact thermal performance and application? This article delves into this subject.
Basic Composition and Working Principle of Thermal Grease
Thermal grease typically consists of silicone oil and fillers. Silicone oil provides the necessary fluidity and adhesiveness, while fillers, such as aluminum oxide, boron nitride, and carbon nanotubes, primarily improve thermal conductivity. These fillers enhance overall thermal performance by increasing the number of thermal conduction paths.
The working principle of thermal grease is relatively straightforward: It fills in the minute gaps between electronic components and heat sinks, reducing the presence of air and thus improving heat transfer efficiency. Air has a low thermal conductivity coefficient; thermal grease, with a significantly higher coefficient, effectively channels heat from components to the heat sink.
Definition and Significance of Specific Gravity in Thermal Grease
Definition Overview: The specific gravity (or density) of thermal grease is a physical concept that denotes the mass of a substance per unit volume, commonly expressed in grams per cubic centimeter (g/cm³). It reflects the compactness of particles within the material and serves as a fundamental parameter for evaluating material properties.
The defining formula is:
Specific Gravity = Mass of Material / Volume of Material
Units for specific gravity include grams per cubic centimeter (g/cm³) or kilograms per cubic meter (kg/m³).
Significance Explanation: In the context of thermal grease applications, specific gravity is not only a vital indicator of material properties but also indirectly relates to thermal conductivity, spreadability, cost-effectiveness, and other characteristics. An appropriate specific gravity helps ensure sufficient thermal conductivity while controlling usage, minimizing costs, and facilitating application, contributing significantly to the stability and longevity of electronic products.
Measuring the Specific Gravity of Thermal Grease
Methods for measuring specific gravity vary, with common techniques including Archimedes' principle, the pycnometer method, and hydrometer measurements.
For thermal grease, measurement can be complex due to its high filler content and multiphase structure. A combination of weighing and volume displacement methods is typically employed to ensure accuracy.
- Pycnometer Method: A common approach involves placing a measured amount of thermal grease in a pycnometer and measuring its mass, then calculating the specific gravity based on the pycnometer's volume.
- Buoyancy Method: Utilizing the buoyancy principle, the specific gravity is calculated by measuring the upward force exerted on the thermal grease in a particular liquid.
- Hydrometer: A specialized density meter directly measures the density of the thermal grease, yielding its specific gravity.
When conducting measurements, factors such as environmental stability (temperature, humidity), sample representativeness, and instrument accuracy must be considered.
Factors Influencing the Specific Gravity of Thermal Grease
The specific gravity of thermal grease is influenced by multiple factors, including composition, filler type and ratio, and manufacturing processes.
- Composition: The ratio of silicone oil to fillers directly impacts the specific gravity. Silicone oil has a lower specific gravity, while fillers generally have higher values. For example, aluminum oxide has a specific gravity around 3.95 g/cm³, and boron nitride is about 2.29 g/cm³. Thus, a higher filler ratio typically leads to a higher specific gravity for the thermal grease.
- Filler Type: Different fillers have varying specific gravities, and selecting different fillers can significantly alter the specific gravity of the thermal grease. Metal oxide fillers, for instance, generally have a higher specific gravity than non-metallic ones.
- Manufacturing Process: Conditions such as mixing homogeneity and filling density also affect specific gravity. Thermal grease prepared under high temperature and pressure tends to be denser, resulting in a higher specific gravity.
Practical Significance of Specific Gravity in Thermal Grease
1. Thermal Performance: While specific gravity is not a direct measure of thermal performance, it correlates to some extent. Generally, thermal grease with a higher specific gravity contains more heat-conducting fillers, suggesting better thermal performance. However, excessively high specific gravity may compromise the material's flexibility and adhesion, negatively affecting heat dissipation.
2. Mechanical Properties: The mechanical properties of thermal grease, like adhesion and flowability, are related to specific gravity. Grease with too high a specific gravity may have poor adhesion, hindering uniform application. Conversely, grease with a very low specific gravity may lack adequate filling capacity, leading to uneven heat conduction.
3. Ease of Use: Specific gravity affects the ease of applying thermal grease. Grease with a high specific gravity tends to be thick and difficult to spread evenly. Grease with a low specific gravity is thinner and flows easily but may require multiple applications to achieve optimal results. Selecting grease with an appropriate specific gravity enhances work efficiency and cooling effectiveness.
Considerations in Application
When selecting thermal grease for practical use, various factors must be balanced:
- Cooling Requirements: High-power density components require high-performance thermal grease, often with a higher specific gravity. However, maintaining adhesion and flexibility is crucial for sustained thermal performance.
- Application Environment: Temperature, humidity, and mechanical vibrations influence the choice of thermal grease. Special environments may necessitate grease with a specific specific gravity to withstand temperature, moisture, and vibration.
- Cost and Performance Balance: High-specific gravity grease tends to be costlier, requiring a balance between performance and cost for an economically efficient cooling solution.
Common Specific Gravity Range of Marketed Thermal Grease
Different brands and models of thermal grease exhibit varied specific gravities. Typically, common thermal greases fall within a range of 1.5 to 3.0. However, this is a broad range, and the exact specific gravity should be determined according to product specifications and application scenarios.
Selecting Suitable Specific Gravity Thermal Grease
- Device Requirements: Choose thermal grease based on the type, power, and cooling design of the electronic device. High-power, high-heat-generating devices may prioritize thermal performance, while devices with weight and space constraints need to balance specific gravity with other properties.
- Testing and Evaluation: Before selection, conduct simple tests and evaluations, including measuring specific gravity, thermal performance, and flow properties. User experiences and reviews can also provide valuable insights.
- Brand and Quality: Opt for reputable brands with reliable thermal grease products to ensure performance and stability. Inferior thermal grease may have inaccurate specific gravity, unstable performance, and negatively impact cooling efficiency and reliability.
Future Development Trends
With the evolution of electronic devices, demand for thermal grease continues to grow. Future trends in thermal grease development include:
- Novel Fillers: The application of nanomaterials and composites will further enhance thermal conductivity and mechanical properties. Carbon nanotube and graphene fillers, for example, could significantly boost thermal efficiency.
- Smart Materials: Smart thermal grease that adjusts its physical properties in response to temperature changes will enable more efficient thermal management.
- Eco-Friendly Materials: With rising environmental standards, developing non-toxic, eco-friendly thermal grease will become a significant focus.
Conclusion
The specific gravity of thermal grease is a crucial physical property impacting thermal performance, mechanical properties, and ease of use. In practical applications, selecting the right specific gravity requires considering cooling needs, environmental factors, and costs. Advancements in technology, including the introduction of new fillers and smart materials, will further enhance thermal grease performance, providing more efficient thermal management solutions for electronic devices. The role of thermal grease in heat dissipation for electronic devices is poised to become increasingly significant in the future.